
[ad_1]
When folks come to my store, they all the time get a tour of the photo voltaic kiln. I inform them it took a few weeks part-time to construct, and the overall supplies price was about $2,500. Inevitably, I’m requested, “Was it value it to construct?” And my reply is all the time, “Sure—I solely want I had constructed it sooner.”
I had spent a few years toying with the thought, doing analysis that might be complicated and too scientific. All of it felt too sophisticated to get began. However after lastly taking the leap, I discovered that constructing and utilizing a photo voltaic kiln isn’t sophisticated in any respect. The kiln is just a well-insulated shed going through south with a passive solar-collecting roof, a black inside to soak up photo voltaic vitality and warmth the air, and followers to flow into it. It operates like an enormous, off-the-grid convection oven sending heated air via your lumber stack, with vents to let evaporated moisture out. That’s it.
A photo voltaic kiln dries lumber in a lot gentler cycles than a industrial kiln. When the solar is out, the heated air circulates, absorbing moisture from the wooden. At night time the lumber cools approach down, the followers are off, and a few of that expelled moisture within the air reabsorbs into the wooden. This sample makes for extra relaxed (and considerably slower) drying in contrast with the fixed stress in a industrial kiln frequently pulling out moisture.
The photo voltaic kiln dries wooden far quicker than air drying alone, and it will get the lumber to a a lot decrease moisture content material. My photo voltaic kiln takes 4 to 5 heat, sunny summer season weeks to dry a load of 5/4 inexperienced wooden to eight% MC. I’ve dried cherry, walnut, ash, purple maple, birch, and oak. It all the time amazes me the standard of lumber that comes out. The wooden has good shade, machines properly, and works fantastically with hand instruments. In my expertise, it behaves a lot better than commercially dried materials; when ripped, it strikes little or no if in any respect.
With a photo voltaic kiln, whether or not you purchase inexperienced planks from a sawmill or have timber sawn on a transportable mill, as I do, your price per board foot will probably be far decrease than shopping for kiln-dried lumber. As well as, some lovely species of timber simply aren’t commercially accessible kiln-dried. And, maybe better of all, having your individual photo voltaic kiln lets you flip a fallen household tree into furnishings. Each venture I construct now comes with a narrative.
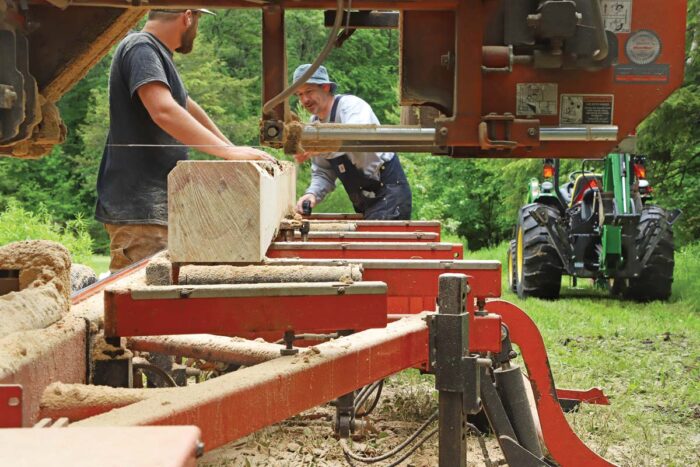
Website and measurement
Finding your photo voltaic kiln is the primary necessary step. You want a spot that has maximal solar publicity, a flat space to construct on, and easy accessibility for loading and unloading. If you happen to don’t have the best spot, the kiln will nonetheless work. Much less solar slows down drying, uneven floor is tougher to construct on, and poor entry makes loading and unloading tougher. However none of these want be a deal-breaker.Determining the roof angle comes subsequent. It’s endorsed the angle of the photo voltaic collector be the identical because the latitude of the situation of the kiln. I’m in West Granby, Conn., at latitude 41.9561°. I made a decision to pitch my kiln’s roof at 45° to make development simpler. Including these few levels additionally provides barely higher leads to the winter.
To maintain my kiln modest in measurement, I selected to make the excessive again wall 8 ft. tall. I deliberate the inside width at 10-1⁄2 ft., so it will match the 8-ft.-plus planks I usually reduce with room to spare. Figuring in a knee wall 3 ft. excessive, these dimensions enable me to dry a most load of roughly 450 bd. ft. That works for me. Measurement your kiln to go well with the masses you need to dry, preserving in thoughts the ratio of photo voltaic collector (the clear, corrugated, greenhouse roofing materials) to board footage to be dried. If the wooden is dried too quick, there will probably be extra defects. The Virginia Tech Cooperative Extension article “Design and Operation of a Photo voltaic-Heated Dry Kiln” is a wonderful total useful resource and significantly useful right here. In keeping with the article, you need 1 sq. ft. of photo voltaic collector for each 10 bd. ft. of 4/4 purple oak within the kiln. There are trade requirements for protected drying charges for various species. Delicate maple will be safely dried a lot quicker than oak. The scale I settled on gave me 70 sq. ft. of photo voltaic collector. This was nearer to 1-1⁄2 sq. ft. of collector per 10 bd. ft., and right here in New England that ratio has labored high quality. There are a number of methods you may regulate your kiln’s every day drying charge.
The construct
I constructed my kiln utilizing commonplace 2x development such as you would see on a backyard shed. I overbuilt the ground deck and the framing in anticipation of the heavy hundreds the ground would help and the chance that I would need to transfer the kiln some day.
I started the construct by flattening the bottom. Then I constructed an oblong body of pressure-treated 2x6s on edge and stuffed it with 1⁄2-in. stone. Subsequent, I positioned three pressure-treated 4×4 beams lengthwise on the stone and leveled them. I assumed having the kiln on skids could be greatest in case I ever do need to transfer it.
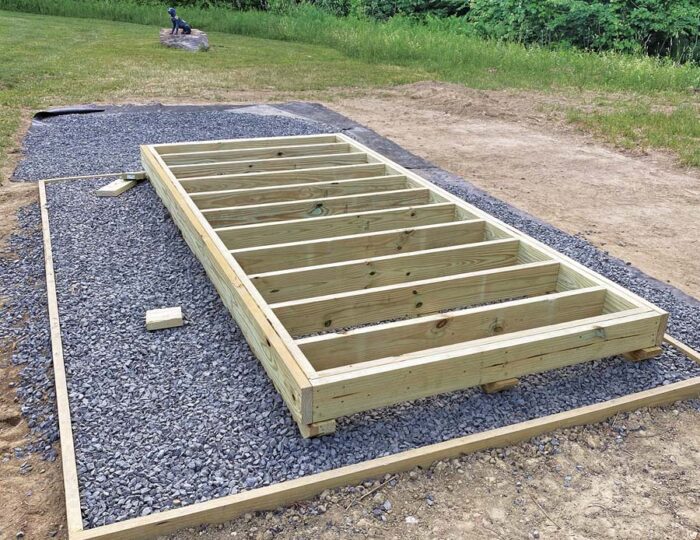
I constructed the deck body on high of the skids, spacing the joists 12 in. on heart and doubling up 2x6s across the perimeter. As soon as the deck body was constructed, I fine-tuned its place so the photo voltaic collector would face exactly south. Then I connected the deck body to the skids under. Between the joists I used doubled-up 2-in. inflexible insulation board and expandable foam that had a complete insulative worth of R-20. For the ground, I used 1⁄2-in. CDX plywood.
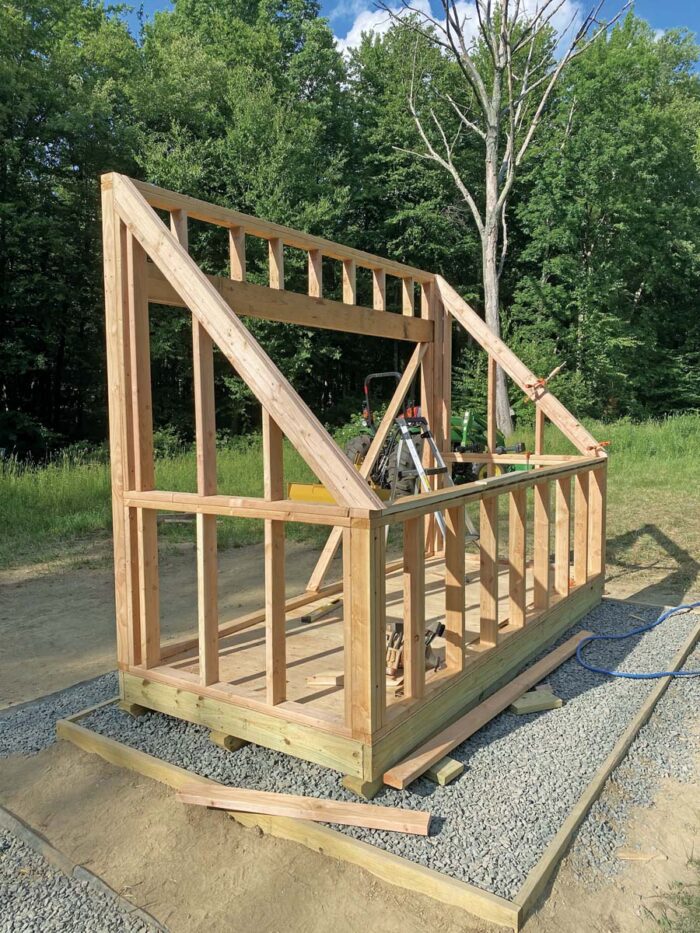
members doubled up for rigidity.
Subsequent I framed the partitions. I wrapped the construction with a vapor barrier and nailed pre-primed T-111 engineered siding to the outside. As soon as the siding was up, I moved into my store to make the doorways. Involved concerning the weight of such massive doorways, I milled down 2x4s to make inventory 1-1⁄4 in. thick by 2 in. large to border the perimeter and the vent openings.
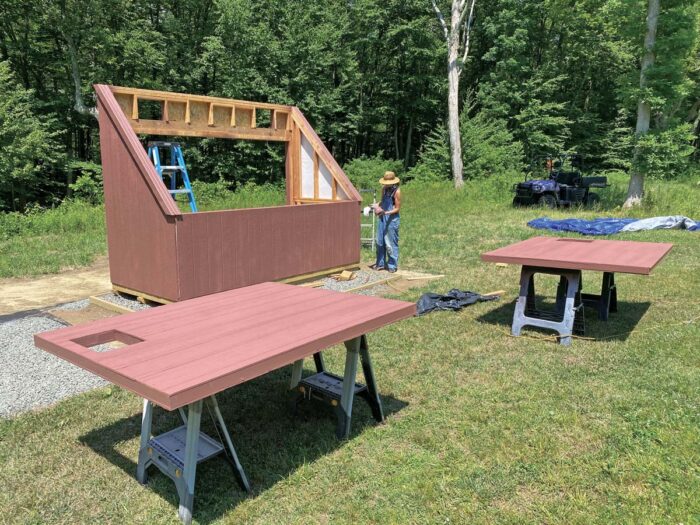
Rubber and roofing
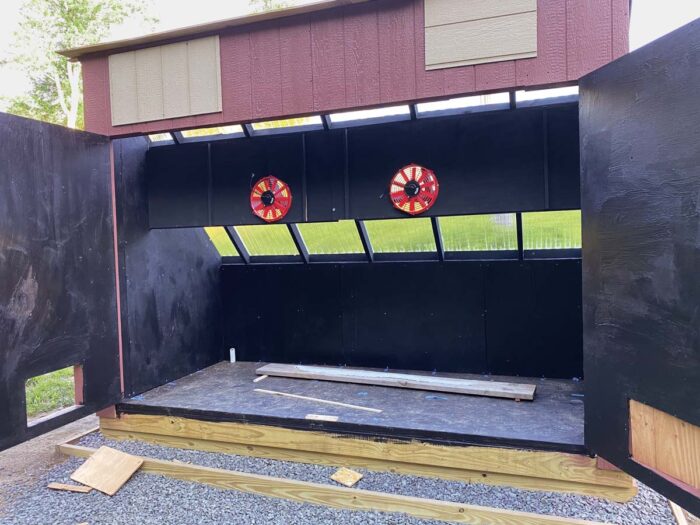
The kiln will get very humid inside throughout the first a number of days of drying inexperienced materials: Water droplets kind on the roof and partitions and even puddle on the ground. To deal with this, the inside of the kiln will get a black rubberized coating that protects the wooden and plywood from moisture. The coating additionally serves as a photo voltaic collector, absorbing warmth from the solar. There are different choices for a black vapor barrier, however I used Black Jack Rubr-Coat 57. It is vitally troublesome to combine and likewise very thick and troublesome to use. I combined it with a mixing attachment on a drill, and as an alternative of portray the CDX plywood inside partitions in place, I pre-cut them and utilized the coating with the items on sawhorses, so I might pour out the coating; I unfold it with disposable brushes. I coated the ground earlier than putting in the wall panels so I might paint proper into the corners and up onto the underside plate of the wall. A 5-gal. pail was simply sufficient for me to do the partitions and ground. For financial system’s sake, I used exterior-grade flat black paint on the rafters.
After insulating the partitions with R-13 kraft-faced fiberglass insulation, I connected the wall panels and sealed all of the seams with black caulk rated for prime temperatures.
Subsequent I connected the pre-painted rafters. As a result of the plastic roofing materials is way thinner than a typical roof, I added horizontal bracing between the rafters.
For the photo voltaic collector I selected a transparent Tuftex polycarbonate greenhouse-rated roof panel accessible at big-box shops. There are a number of choices for greenhouse-rated panels that may work as a passive photo voltaic collector.
The 2 followers that flow into air via the lumber stack are vital to the kiln’s operation. Followers made to tolerate excessive temperatures can get dear, however I opted for an inexpensive and easy pair of plastic automotive radiator followers. They’re 12-volt followers rated at 875 cfm every. They supply loads of airflow for my measurement kiln and don’t have any hassle tolerating fluctuations in energy. After 4 years they’re working flawlessly.
I don’t have energy accessible to the kiln, so I energy my followers with two photo voltaic panels. When the solar is out, the followers spin. Easy as that. They even spin on cloudy days, simply not as quick. The photo voltaic panels are every 100-watt monocrystalline panels that have been simple to put in and wire on to the followers.
In lots of solar-kiln designs the followers are connected completely. However that makes it awkward to load and unload the kiln. I hung the followers on 1⁄4-in. plywood supported by a French cleat. When it’s time to load or unload, I merely unplug and take away the followers (device free) and set them apart.
If you happen to construct a photo voltaic kiln, I hope you benefit from the strategy of constructing—and of drying your individual wooden. Let the drying start!
—Brenon Plourde dries and works wooden in West Granby, Conn.
Join eletters right now and get the newest strategies and how-to from Effective Woodworking, plus particular gives.
Obtain FREE PDF
whenever you enter your e mail deal with under.
[ad_2]